Laboratories and Facilities
The Frank H. Dotterweich College of Engineering occupies four separate buildings with a combined floor space of almost 130,000 square feet. This space includes an 80,400 square feet Engineering Building that became operational in August 2001. This building has proven to be an exceptional teaching facility.
The primary ME administrative spaces include 923 square feet for offices and a 154 square foot workroom, both located on the third floor of the main engineering building and shared with the Chemical and Electrical engineering departments.
The department chair has a 200 square foot office off of the main administrative office. Faculty offices, also located on the third floor, are ~140 square feet each. Additionally, there is a 776 square foot Faculty Lounge with a refrigerator, two microwaves, a sink, and vending machines. There is an outdoor patio/balcony outside the Faculty Lounge. There is also a 100 square foot instructor office in the McNeil.
The computer system administrator has a 156 square foot office with an adjoining 88 square foot room for the server and storage. Additionally, there is a 415 square foot room supporting the multimedia and TTVN needs of classrooms 136 and 138.
The 1200 square foot machine shop is located in the McNeil Engineering Lab Building.
The Frank H. Dotterweich College of Engineering provides excellent classrooms in the main engineering and McNeil buildings. There are seventeen classrooms available with a combined space of over 13,000 square feet, each seating between 15 and 87 students. All classrooms provide multimedia support including computers, projectors, and high-speed internet connections. Five of the classrooms have computers for use by the students, complete with internet access and a complete complement of software.
The main engineering building also has 725 square feet for Javelina Engineering Student Success Center(
Summary of classroom space used by the ME Department
Building and Room Number |
Maximum Seating |
Building and Room Number |
Maximum Seating |
McNeil 302 |
24 |
ENGC 109 |
87 |
McNeil 308 |
59 |
ENGC 112 |
24 |
Gross Hall 108 |
40 |
ENGC 113 |
39 |
Gross Hall 109 |
40 |
ENGC 136 |
45 |
Gross Hall 110 |
44 |
ENGC 138 |
42 |
Gross Hall 111 |
33 |
ENGC 218 |
44 |
ENGC 104 |
40 |
ENGC 207 |
15 |
ENGC 106 |
36 |
ENGC 275 |
64 |
ENGC 107 |
32 |
|
|
Additionally, all other classrooms on campus are available as needed to accommodate larger classes and more sections.
The ME Department has eight laboratories--Engineering Measurements, Materials Science, Fluids/Thermal, Manufacturing Processes, Composites, Robotics, Controls, Automation & Simulation, and a machine shop. All labs in addition to the courses they are tied with, also support Senior Design (MEEN 4263 & 64) work as well as ongoing research. These labs are located in Engineering Complex (EC), Dotterweich (Dott), and gross Hall.
MEIE Laboratories
Laboratory Name |
Room # |
Courses & Instructor |
Equipment |
Engineering Measurements |
McNeil 301 |
MEEN 2146 – Rajashekar Mogiligidda MEEN 4263/4264 – Grady Isensee |
Thermocouples, strain gauges, pressure transducers, pressure gauges, LVDT’s, load cells, data acquisition systems, viscosity, Arduino boards, and flow measurements. |
Materials Science |
Dott 208 |
MEEN 3145 – Mohammad Hossain MEEN 4385 – Larry Peel MEEN 4263/4264 – Grady Isensee |
A universal testing machine, impact test machine, fatigue (both reverse bending and torsional) testing, hardness testing, creep testing, polishing stations, scratch testing machine, a high-temperature oven, and a metallurgical microscope. |
Fluids/Thermal |
Dott 207a |
MEEN 4131- Sangsoo Lee |
Thermodynamics, heat transfer, and fluid mechanics equipment are available including two different sized wind tunnels, thermal property analysis and demonstration equipment for convection heat transfers, heat exchangers, and a hydraulic system for Bernoulli’s law and venturi meter. |
Composites Fabrication |
Dott 207b |
MEEN 4385 – Larry Peel MEEN 3349 – Larry Peel MEEN 4263/4264 – Larry Peel |
A three-axis Entec-CMC filament winder, a 33 ft3 Grieve curing oven, a large self-healing cutting table with a rack, an air compressor, a vacuum pump, and a heated platen press. A portable OROS 4 channel digital data acquisition system, OROS software, an instrumented hammer, several accelerometers, and a “Visual Modal” software package, and a new multi-material Stratasys Connex 500 3d printer. |
Manufacturing Processes |
EC 219 |
MEEN 3349 – Larry Peel MEEN 4385 – Larry Peel MEEN 4263/4264 – Larry Peel |
A new large Tormach CNC mill, a smaller desktop CNC mill, several new 3D printers, and several computer workstations. Another new multi-material 3D printer is located in Dott 207b. A new micro-milling machine is located in this lab. |
Robotics |
EC 249 |
MEEN 4355 – Selahattin Ozcelik MEEN 4344 – Selahattin Ozcelik MEEN 4371 – Selahattin Ozcelik MEEN 5335 – Selahattin Ozcelik |
The lab has an iRobot Programmable Robot, Pioneer P3-DX Mobile Robot, Khepera Mobile Robot, Robotic Arm Manipulator, Humanoid Arm, and Five Computers. |
Controls |
EC 250 |
MEEN 4355 – Selahattin Ozcelik MEEN 4344 – Selahattin Ozcelik MEEN 4371 – Selahattin Ozcelik MEEN 5335 – Selahattin Ozcelik |
The lab has a Quanser Heat Flow Chamber, a Water Level Control Setup, a DC Motor Speed Control Setup, a Rotary Servo Motor Setup, a Rotary Torsion Setup, Five Quanser Data Acquisition Boards, a PLC Trainer System, an Electro-Dynamic Shaker, a Keysight Waveform Generator, Mixed-Signal Oscilloscope, MXA Signal Analyzer, Eight Power Supply Instruments, a National Instruments Elvis Station, a Light Source Following Antenna System, and Seven Computers. |
Design & Simulation |
INDT 115 |
MEEN 3360 – Shah Alam MEEN 3398 – Xue Yang MEEN 4395 – Xue Yang MEEN 4396 – Xue Yang MEEN 4263/4264 – Grady Isensee |
The lab has 6 Dell Precision Towers, 6 Dell Optiplex desktops, Dell PowerEdge Rack Server, 4 Canberra Lab kits, 4 Programmable Logic Controllers (PLC) controllers, and workstations. |
The Engineering Measurements Lab supports the MEEN 2146 Engineering Measurements course. Thermocouples, strain gauges, pressure transducers, pressure gauges, LVDT’s, load cells, data acquisition systems, viscosity Arduino boards, and flow measurements, and other related equipment are available. The lab manager for the Engineering Measurements lab is Rajashekar Mogiligidda. The lab has been updated with new equipment, and additional new NI Elvis Prototyping Boards, new Labview Software, and 5 new computers have been installed. The lab is in room 301 of the McNeil Engineering building and includes 1000 square feet.
Engineering Measurements Lab
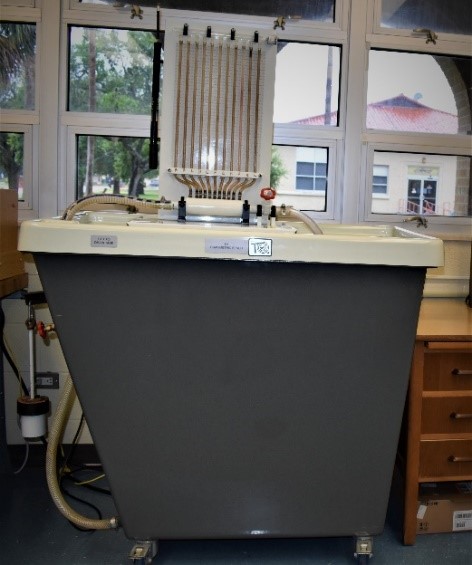
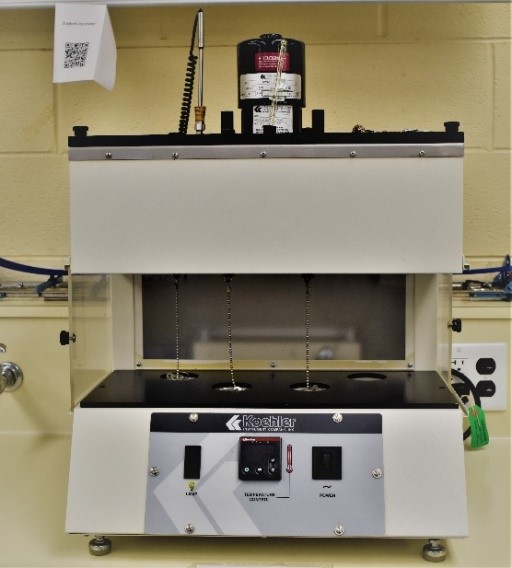
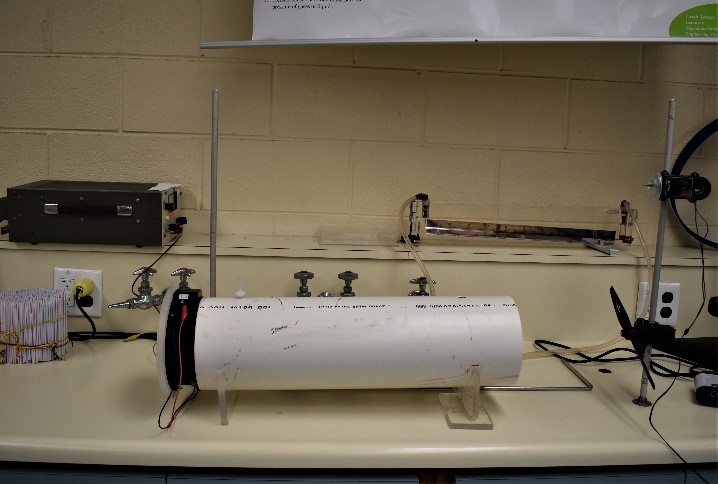
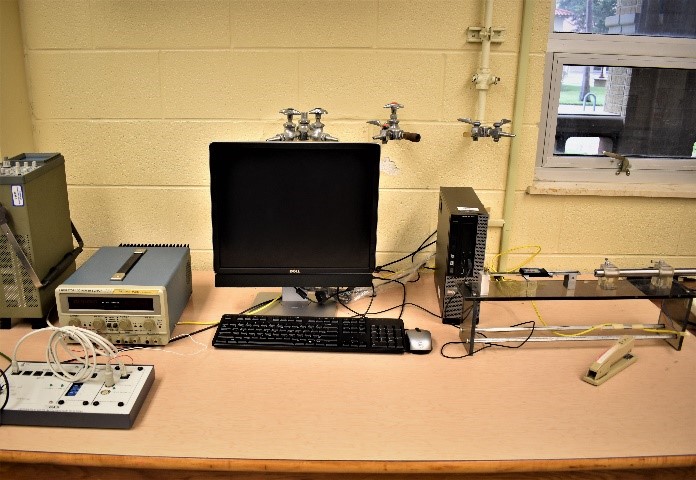
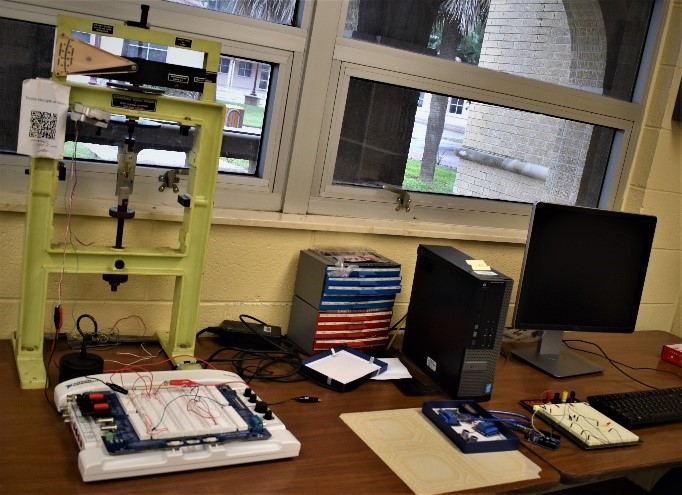
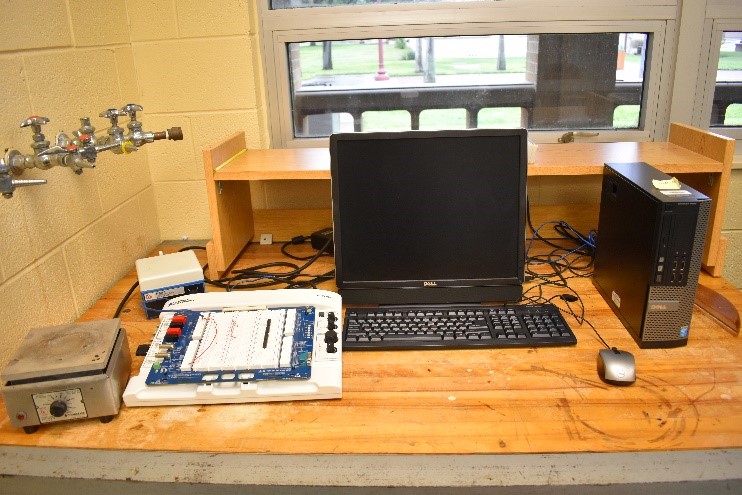
The Materials Science Lab supports MEEN 3145 Materials Science Laboratory course. Materials testing equipment such as the universal testing machine, impact test machine, fatigue (both reverse bending and torsional) testing, hardness testing, creep testing, polishing stations, scratch testing machine, a high-temperature oven, and a metallurgical microscope are available. The lab manager for the Materials Science lab is Dr. Mohammad Hossain. The lab is located in room 208 of the Dotterweich building and includes 1036 square feet.
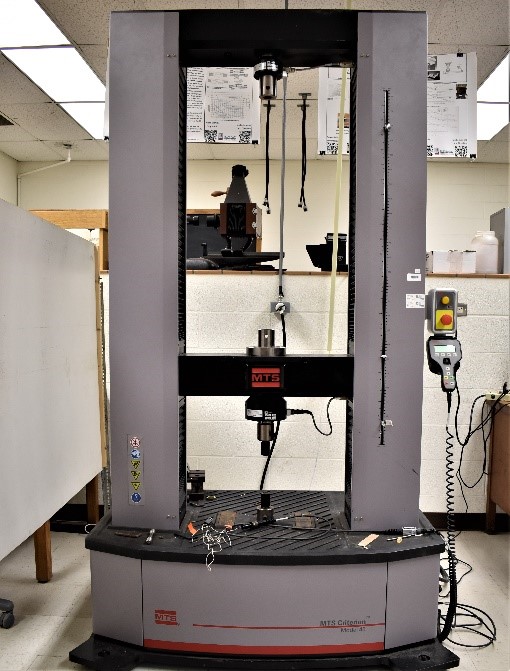
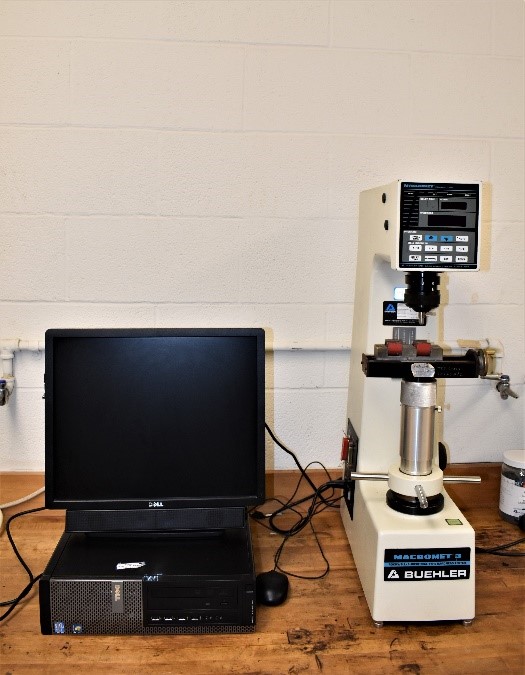
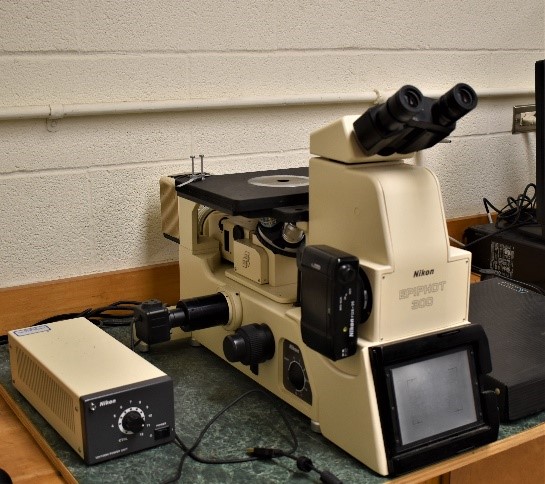
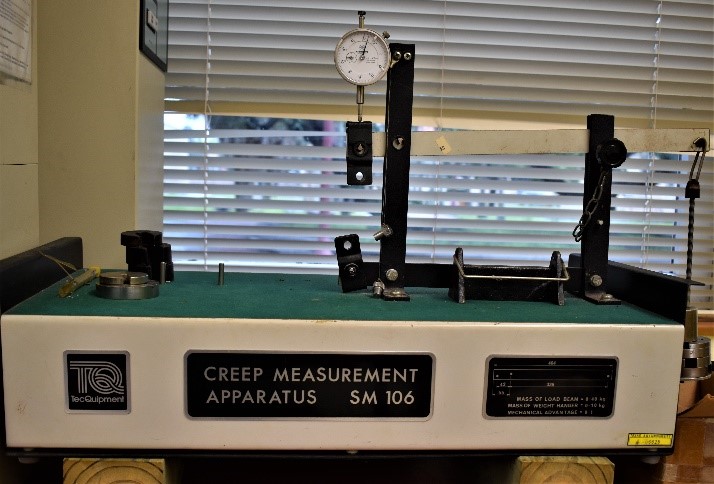
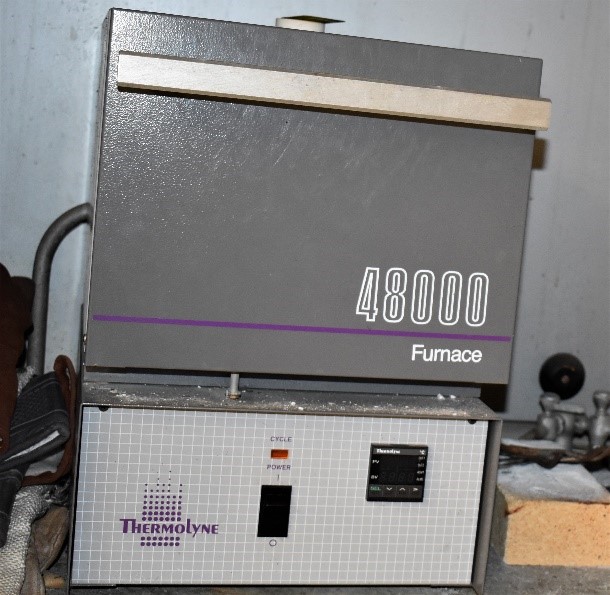
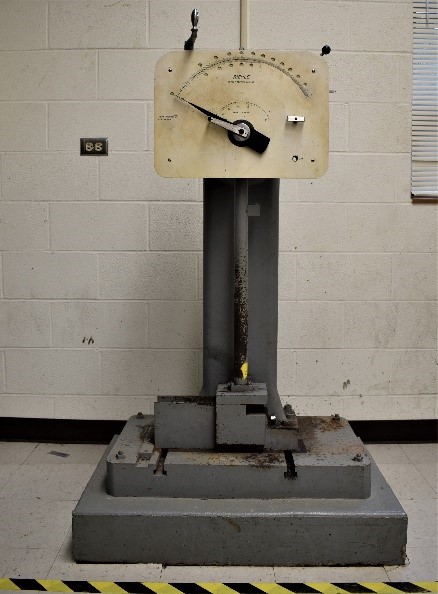
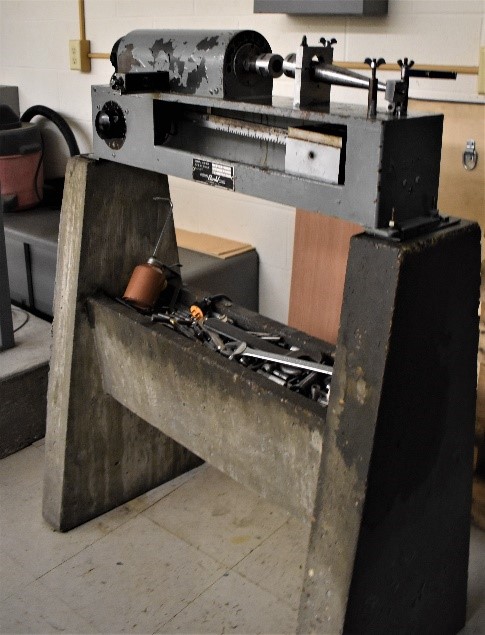
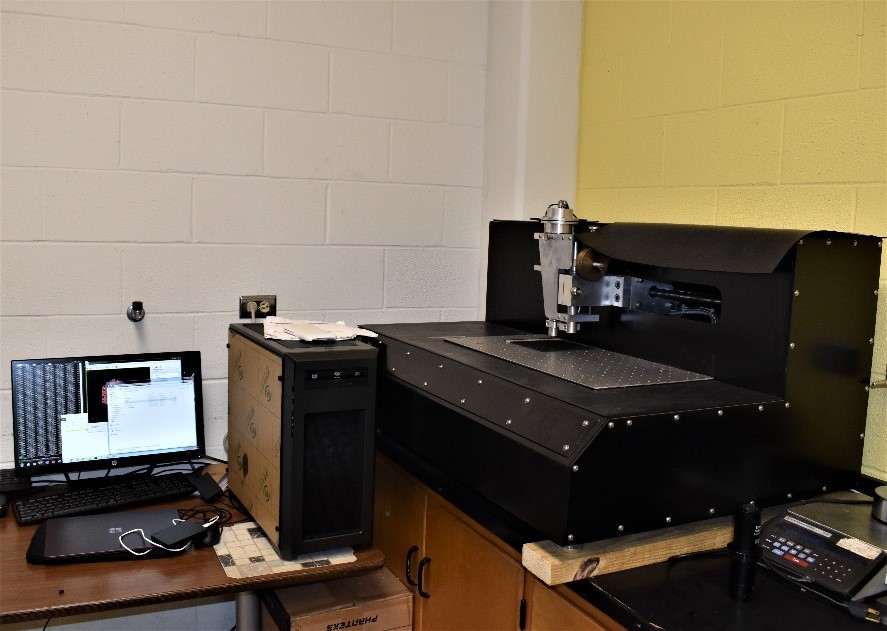
The Fluids/Thermal Lab supports MEEN 4131 Mechanical Engineering Laboratory course. Thermodynamics, heat transfer, and fluid mechanics equipment are available including a wind tunnel and demonstration equipment for heat exchangers, conduction heat transfer, thermal radiation, and convection heat transfer. The thermal and fluid laboratory is located in room 207 (12.9 m x 7.7 m) in Dotterwich College. The thermal and fluid Lab is managed by Dr. Lee. It currently holds 2 wind tunnels, demonstration units for 6- pass heat exchanger, convective heat transfer, hydraulic system, and thermal conductivity measurement unit. Undergraduate students significantly use the lab equipment for Mechanical Engineering Laboratory (MEEN 4131) and currently, Dr. Lee is working on developing sustainable thermal energy systems using nano/micro technologies for system and component levels.
- Wind Tunnels: The wind tunnel (Hampden Engineering, model H-6910) shown in Figure below has been designed to provide the fundamental airflow facilities necessary to perform any experiments to test fluid flow over a surface or check the aero dynamicity of different objects.
- Convection Heat Transfer Demonstrators: The Laboratory currently holds 2 convection experiment setups (Hampden Engineering, model H-6860) shown in Figure below. These setups are to demonstrate the phenomenon of forced and natural convection heat transfer. The setups come along with a variety of shapes and sizes of cylinders and flat plates to show the effect of surface area and geometries of heating elements on convection heat transfer performances. Using these experiment setups, several convective heat transfer tests can be conducted including forced convection heat transfer experiments over a cylinder and a flat plate and natural convection over the vertical plate.
- Heat Exchanger Apparatus: The heat exchanger apparatus (Hampden Engineering, model H-6878) shown in Figure below is for the obtaining effectiveness of various kinds of heat exchangers by exchange heat between hot and cold fluids. The heat transfer performances of several types of heat exchangers can be evaluated and compared and the key parameter to improve effectiveness can be observed using the test setup.
- Hydraulic System Demonstrators: The lab has hydraulic system (Gunt, HM150) test setups for a Venturi meter (Gunt, HM150.13) and a piping system (Gunt, HM150.11) shown in Figure below. The Venturi meter is used to measure a flow rate and the piping system is used to demonstrate several friction losses in a piping system including pressure losses due to various types of bends, extractions, and expansions. These experiment setups are used for understanding the fundamentals of pressure losses of viscous fluids in a piping system and measuring flow rate.
- Thermal Conduction Demonstrators: Thermal property analysis (Setaram: C-Therm TCi) shown in Figure below is used to obtain thermal conductivities of various types of solids in single and/or stacked cylinder-type solid materials.
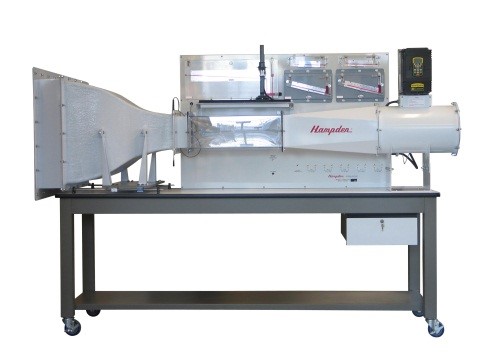
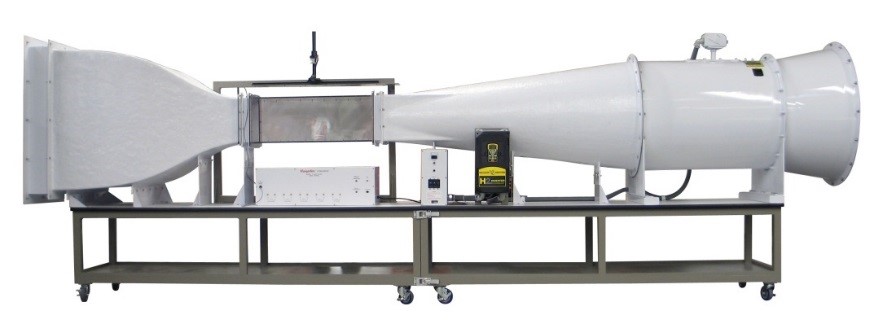
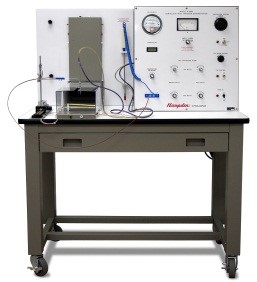
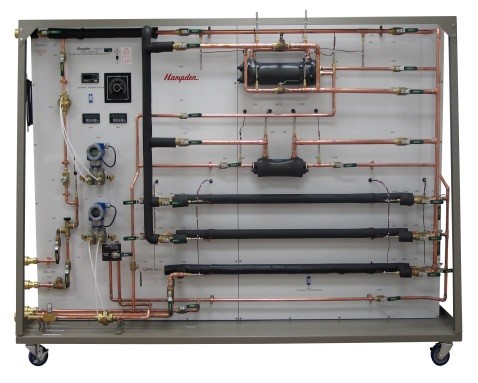
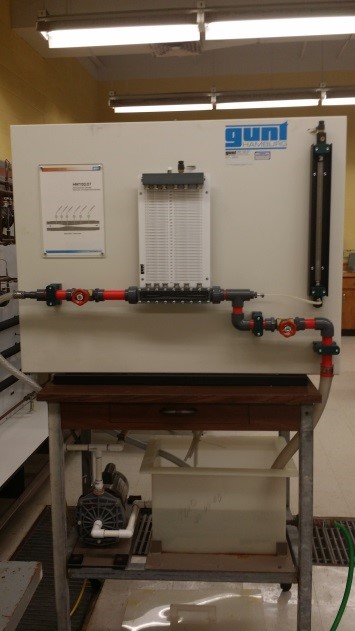
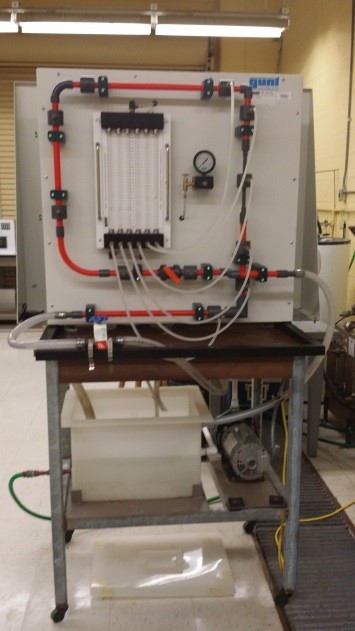
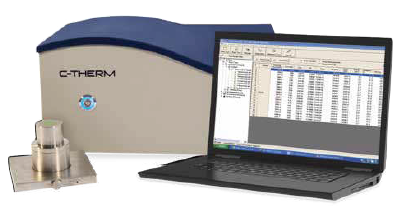
The Manufacturing Processes Lab supports the MEEN 3349 Fundamentals of Manufacturing Processes course and MEEN 4385 Manufacturing of Composites course. This lab is used for lecturing, demonstration, and hands-on work and includes a new large CNC mill, a smaller desktop CNC mill, several 3D printers, and several computer workstations. Another multi-material 3D printer is located in Dott 207b. The lab manager for the Manufacturing Processes lab is Dr. Larry Peel. The lab is located in room 219 of the main engineering building and includes 723 square feet.
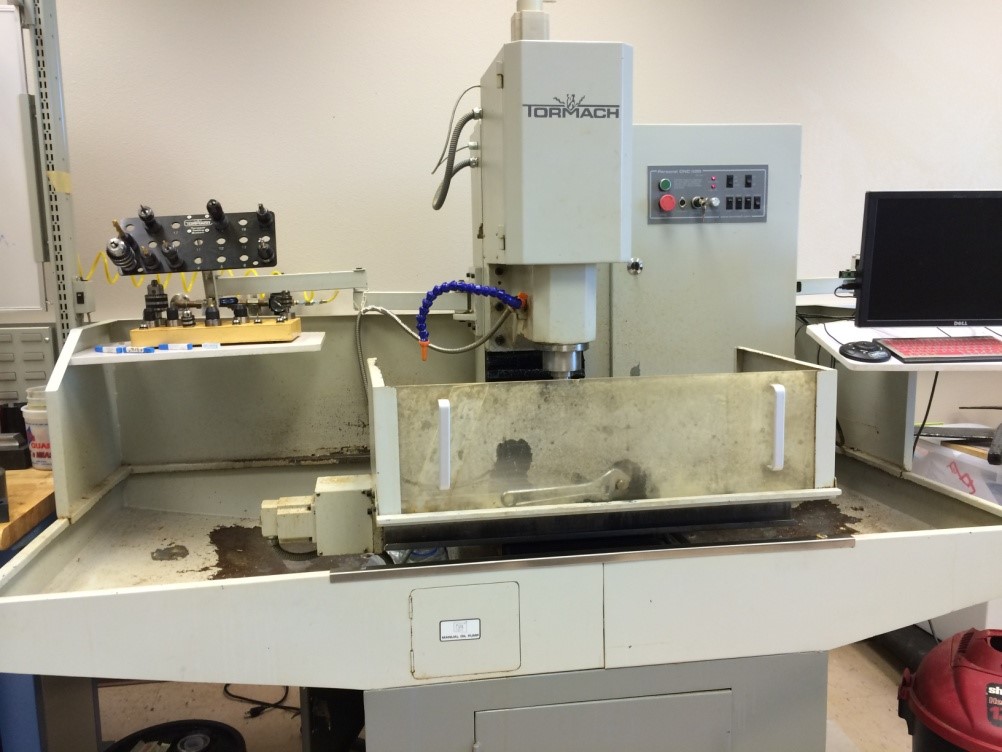
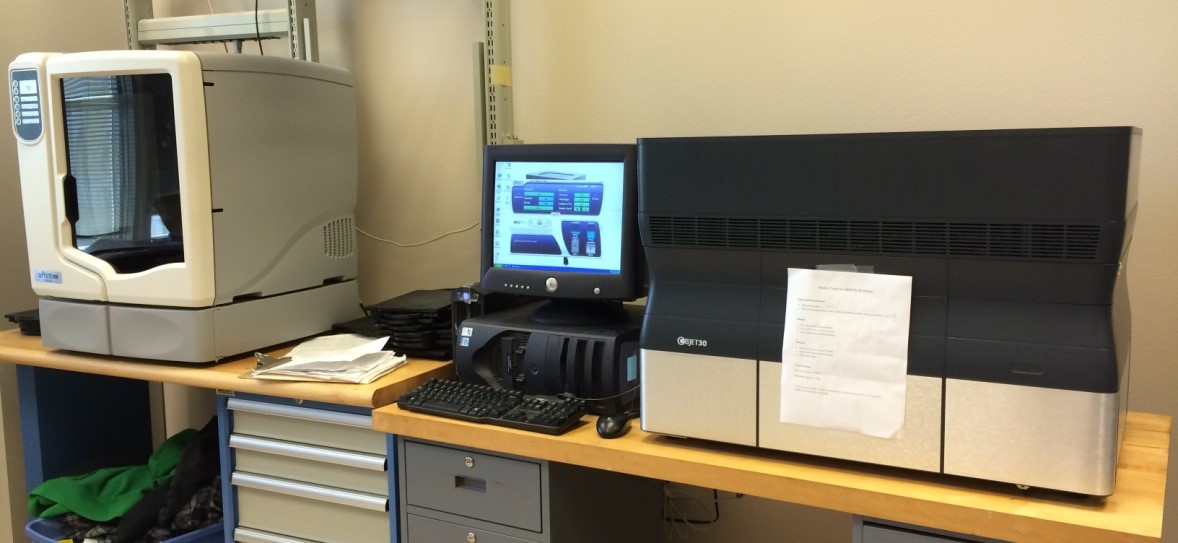
The Composites Lab supports the MEEN 3349 Fundamentals of Manufacturing Processes course and MEEN 4385 Manufacturing of Composites course. The laboratory provides advanced composites fabrication capabilities that are not found elsewhere in south Texas and is one of the better-equipped university composites fabrication labs in Texas. The lab has a three-axis Entec-CMC filament winder, a 33 cubic foot capacity Grieve curing oven, a large self-healing cutting table, a rack for rolls of carbon and fiberglass cloth, an air compressor, a vacuum pump, and the latest addition to the lab, a heated platen press from Carver featuring two 12”x12” platens that can be heated up to 450 Fº, a stroke of 5.5 inches, and 20 tons clamping force. Vibration testing is conducted using a portable OROS 4 channel digital data acquisition system, OROS software, an instrumented hammer, several accelerometers, and a “Visual Modal” software package installed on a laptop that allows students to extract natural frequencies and damping values. The latest addition to the lab, installed in Spring 2014 is a multi-material Stratasys Connex 500 3d printer. The lab manager for the Composites lab is Dr. Larry Peel. The lab is located in room 207B of the Dotterweich building and includes 991 square feet.
Entec-CMC 3 Axis Filament Winder
The three-axis Entec-CMC filament winder has a fiber tensioner with wet- and dry-winding of parts up to 8 feet in length and 24 inches in diameter. The winder is linked to a computer workstation where “FibergrafiX Plus” is used to create winding patterns.
Cutting Table (Left) and Vacuum Pump for Vacuum Bagging (Right)
The lab has a 33-cubic foot capacity Grieve curing oven that will cure large parts up to 400°F. This oven has ports built into it so that vacuum bags and resin infusion equipment can be used inside the oven.
A-33 Cubic Foot Oven (Left) and Vibration Testing Equipment (Right)
Vibration testing is conducted using a portable OROS 4 channel digital data acquisition system, OROS software, an instrumented hammer, several accelerometers, and a “Visual Modal” software package installed on a laptop that allows students to extract natural frequencies and damping values.
Heated Platen Press
A very useful addition to the lab is a heated platen press from Carver. It has two 12”x12” platens that can be heated up to 450 Fº, with a stroke of 5.5 inches, and can apply 20 tons clamping force. The press can be used to mold plastic and composite parts.
Flammable liquids are stored in an OSHA-approved cabinet, in a large storage room with shelves and cabinets for student projects.
Stratasys CONNEX 500 Multi-Material 3D Printer
The Robotics Lab supports the MEEN 4355 Robotics and Automation course, as well as graduate courses and graduate research. The Robotics lab has an iRobot Programmable Robot, Pioneer P3-DX Mobile Robot, Khepera Mobile Robot, Robotic Arm Manipulator, Humanoid Arm, and five computers. The lab manager for the Robotics lab is Dr. Ozcelik. The lab is located in room 249 of the main engineering building and includes 700 square feet.
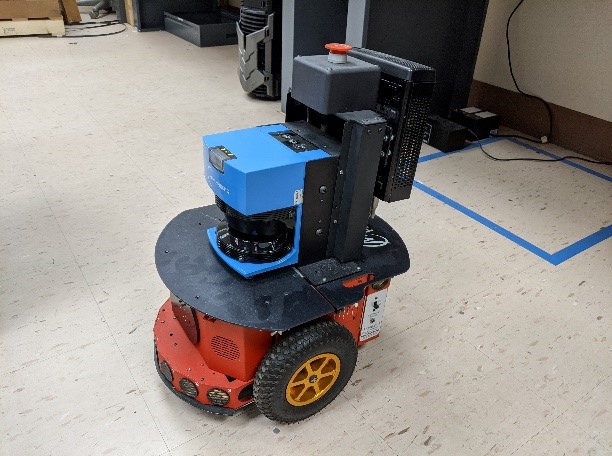
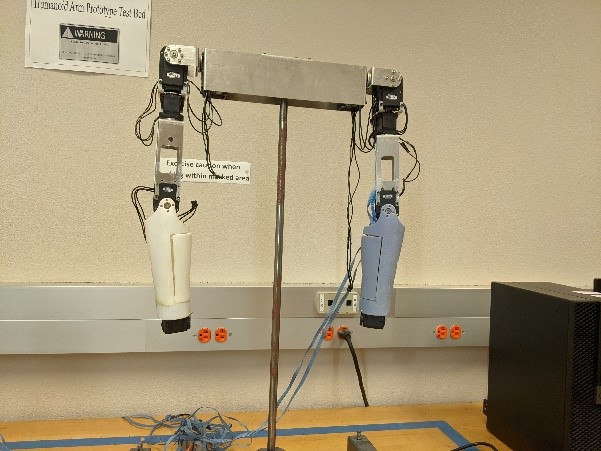
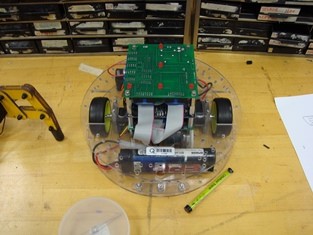


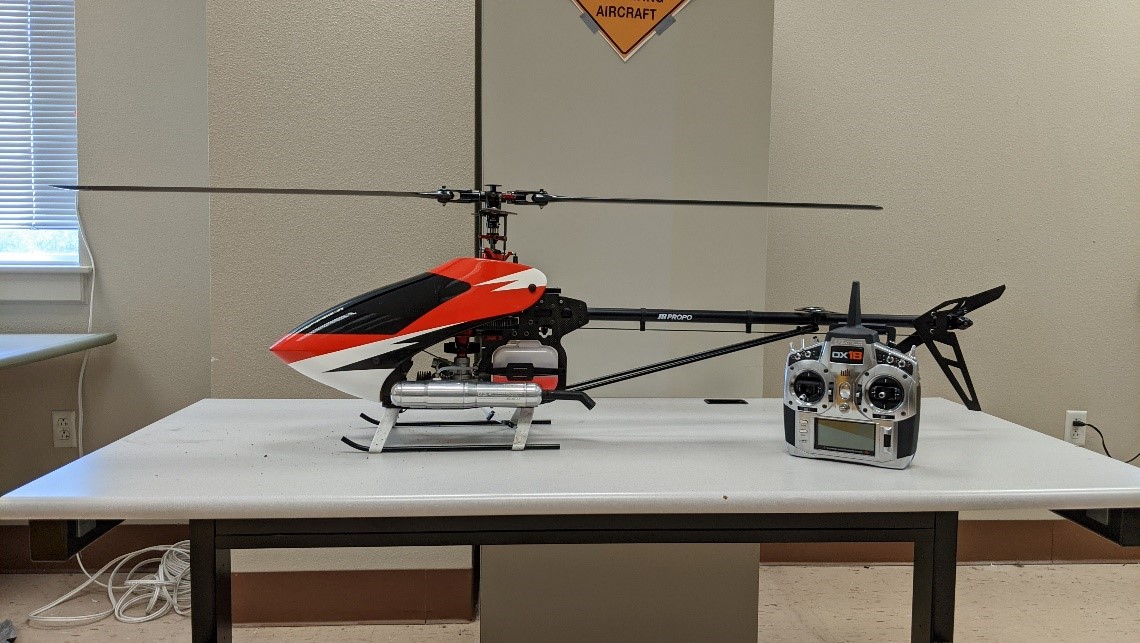
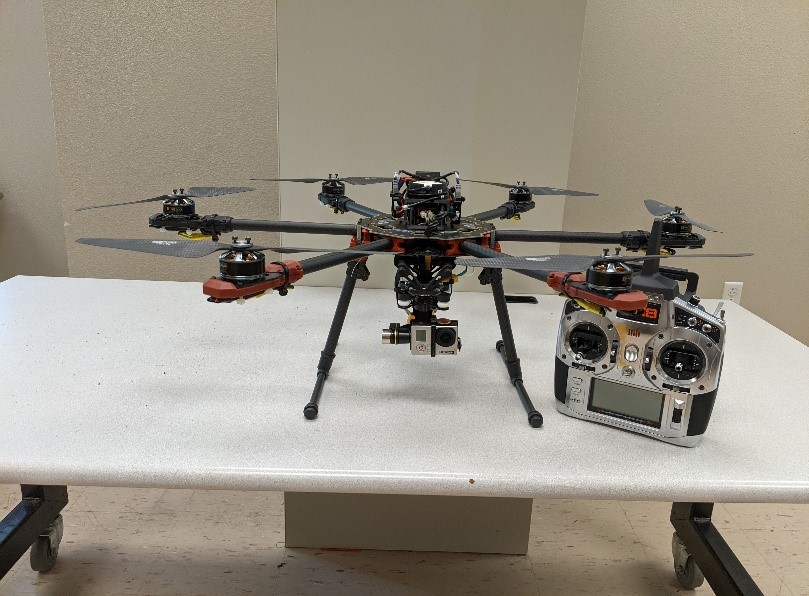
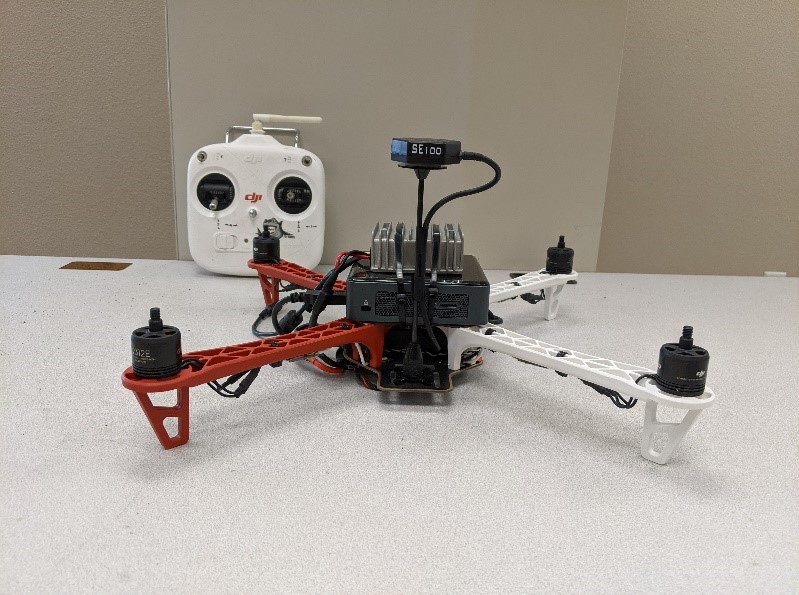
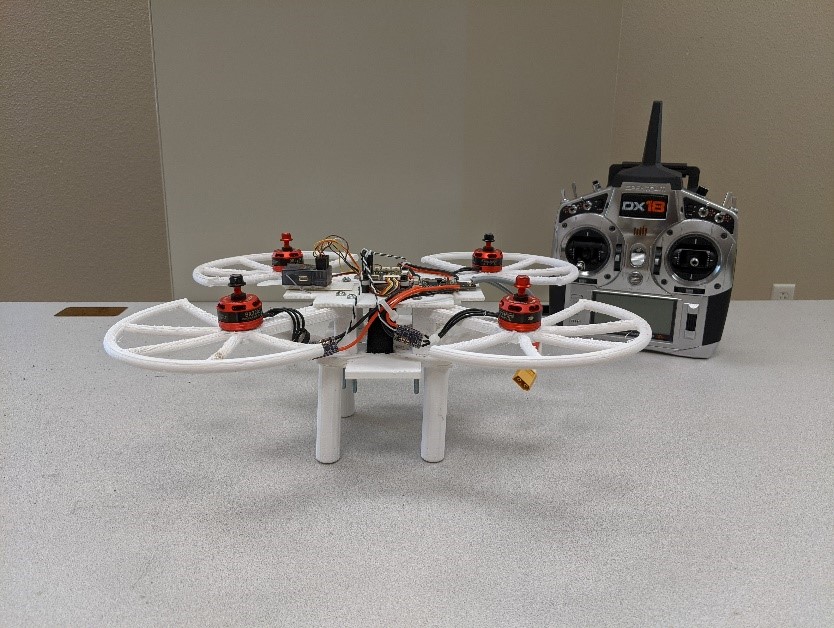
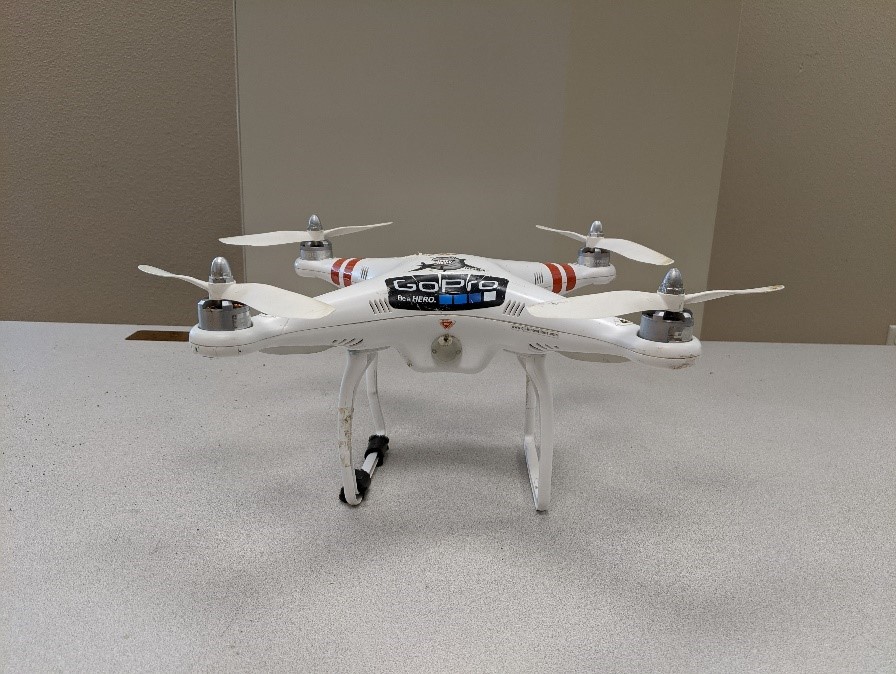
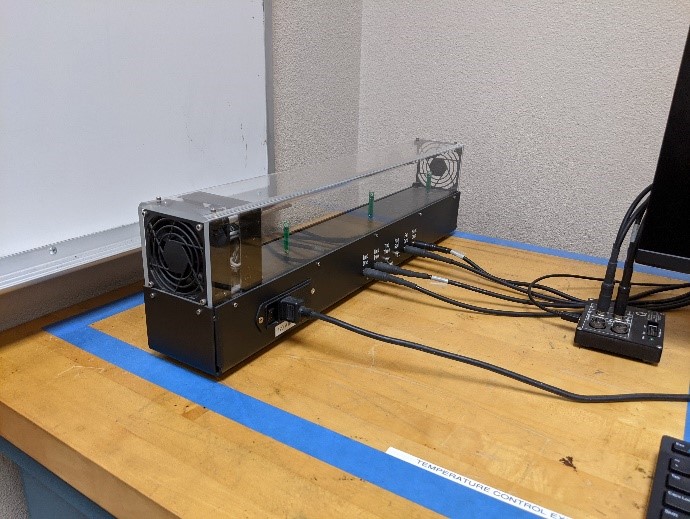
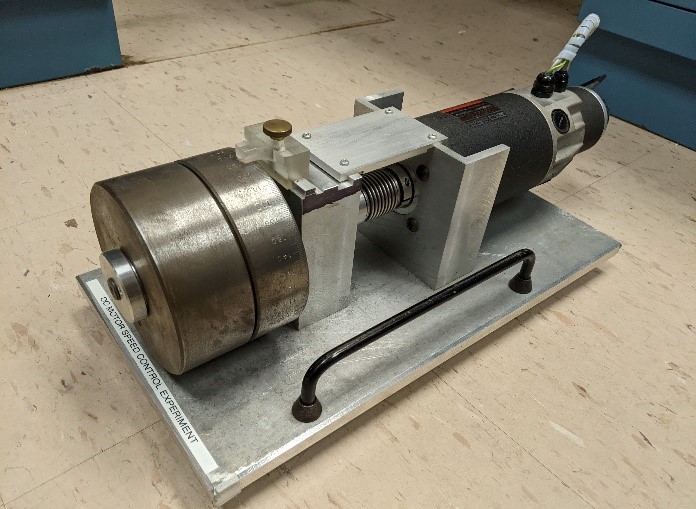
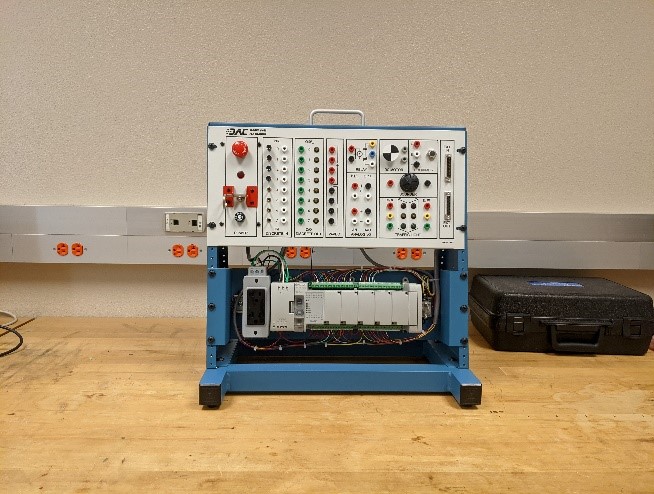
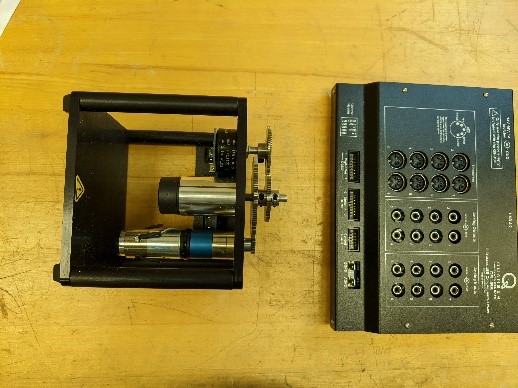
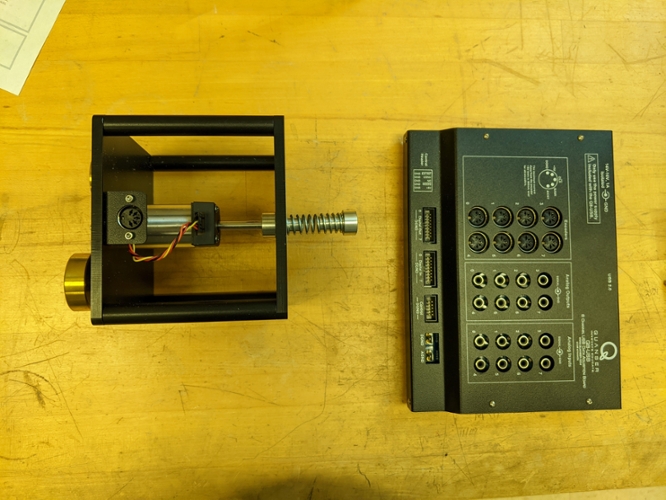
The Controls Lab supports the MEEN4344 Control of Systems course, as well as graduate courses and graduate research. The lab has a Quanser Heat Flow Chamber, a Water Level Control Setup, a DC Motor Speed Control Setup, a Rotary Servo Motor Setup, a Rotary Torsion Setup, Five Quanser Data Acquisition Boards, an Electro-Dynamic Shaker, a Keysight Waveform Generator, Mixed-Signal Oscilloscope, MXA Signal Analyzer, Eight Power Supply Instruments, a National Instruments Elvis Station, a Light Source Following Antenna System, and Seven Computers. The lab manager for the Controls lab is Dr. Ozcelik. The lab is located in room 250 of the main engineering building and includes 636 square feet.
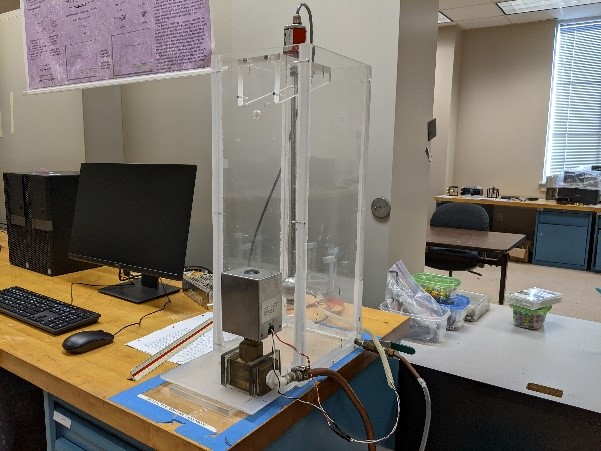
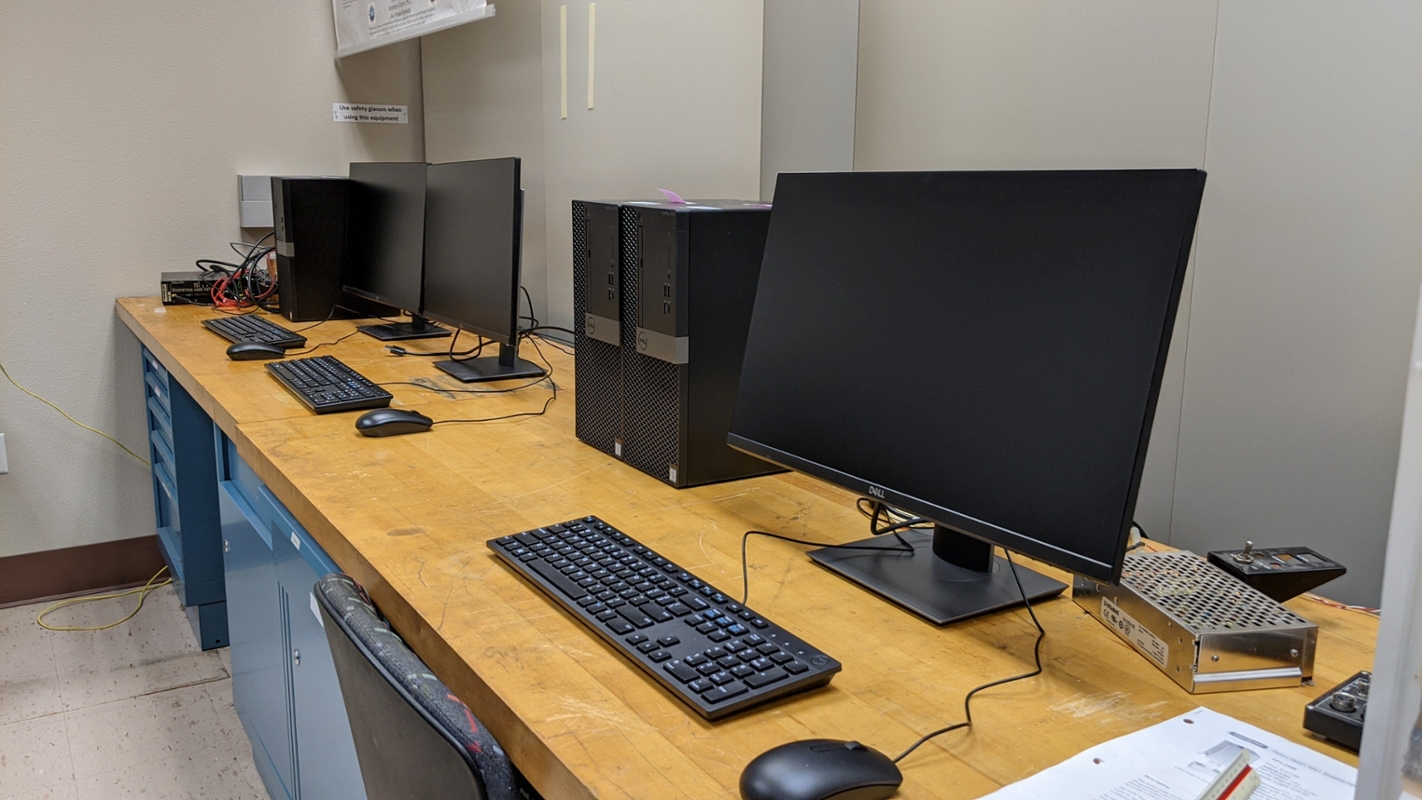
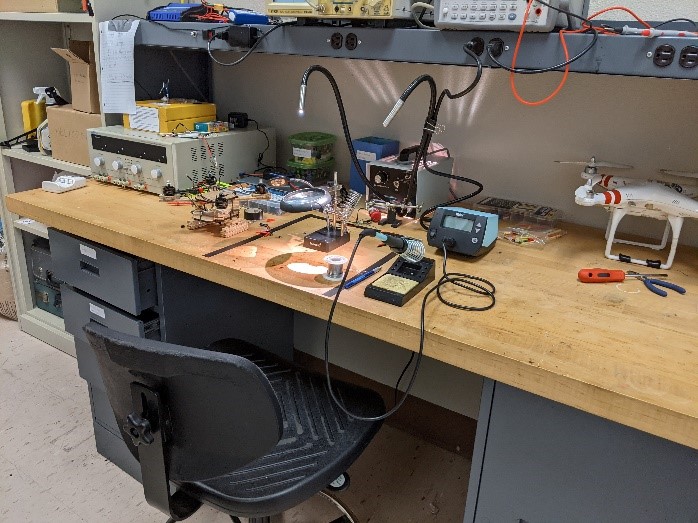
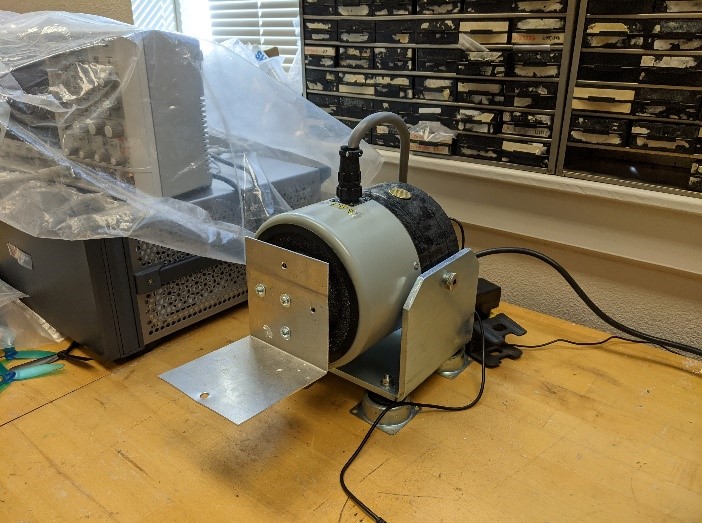
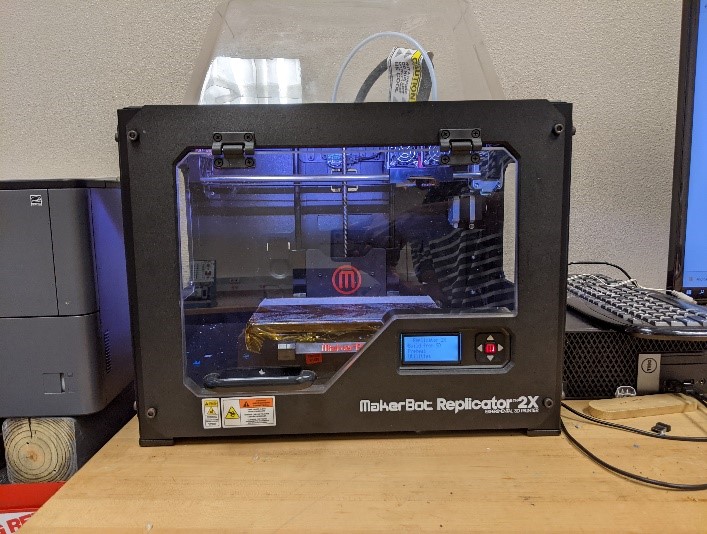
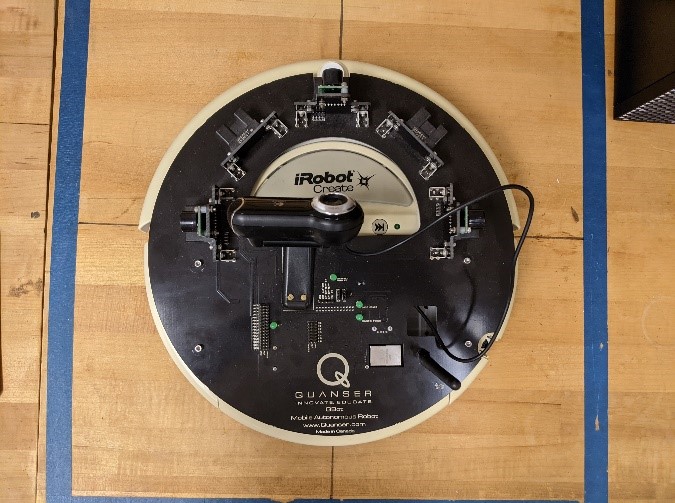
The Design and Simulation Lab supports the MEEN 3360 Engineering Design and Simulations course, MEEN 4263/4264 Mechanical Engineering Design Projects I/II Courses, MEEN 3398 Computer Applications in Nuclear Engineering, and MEEN 4395 Thermal Hydraulics of Nuclear Reactors. The lab is located at Industrial Technology Building room 115 and includes 950 square feet. This lab is used for lecturing, demonstration, and hands-on work on the Programmable Logic Controllers (PLC). The lab includes four PLC workstations and four computer workstations. Nuclear simulation courses are conducted in this lab. Mechanical engineering senior design students use this lab for design calculations and simulations.
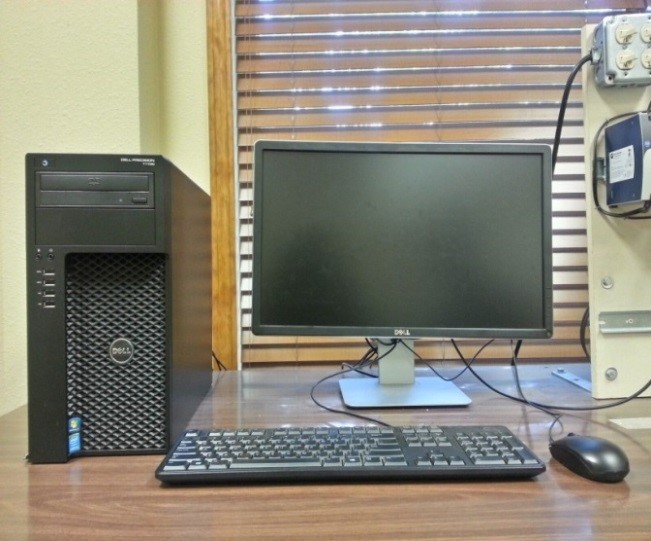
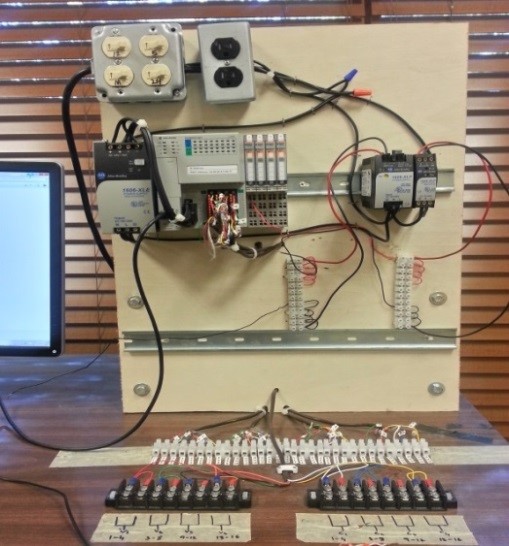
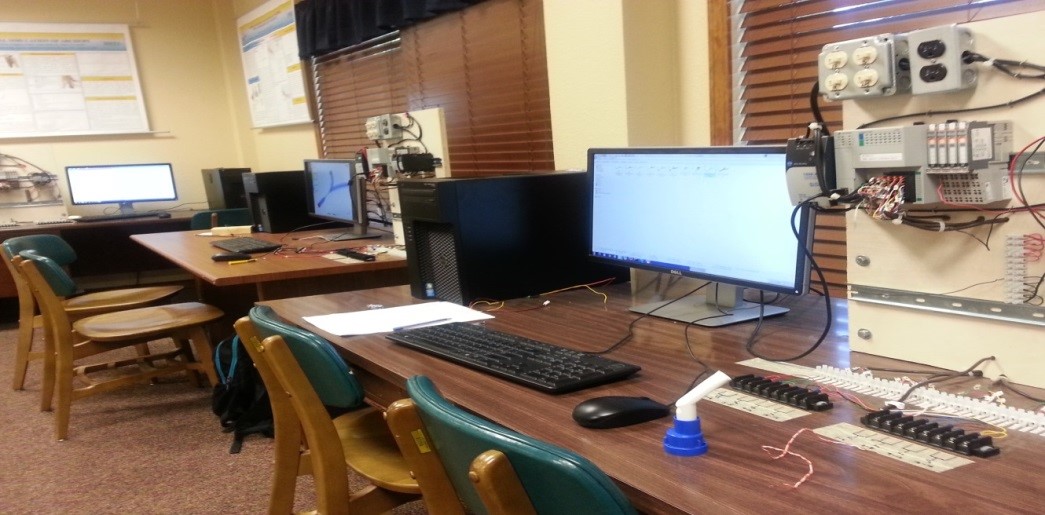
The Mechanical Engineering Department of TAMUK has a well-equipped machine shop and a full-time machinist. The machine shop is located in room 301 within the McNeil Building. Equipment in the machine shop includes several lathes, a milling machine, a table saw, band saws, drill presses, welding machines, a surface grinder, and other special-purpose tools. The machine shop is available for full use by students and faculty. Many Senior Design teams fabricate items in the machine shop, with the support of the machinist.
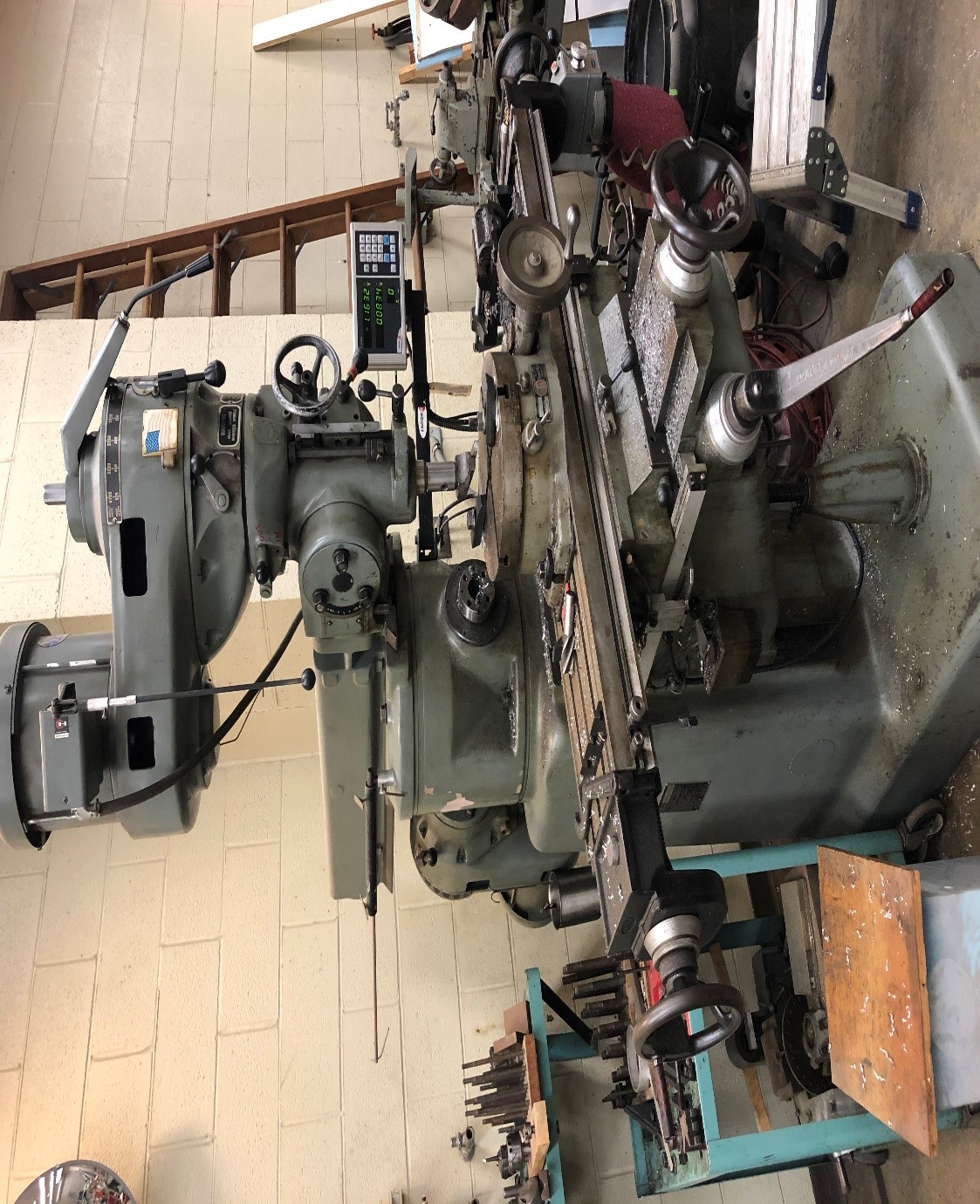
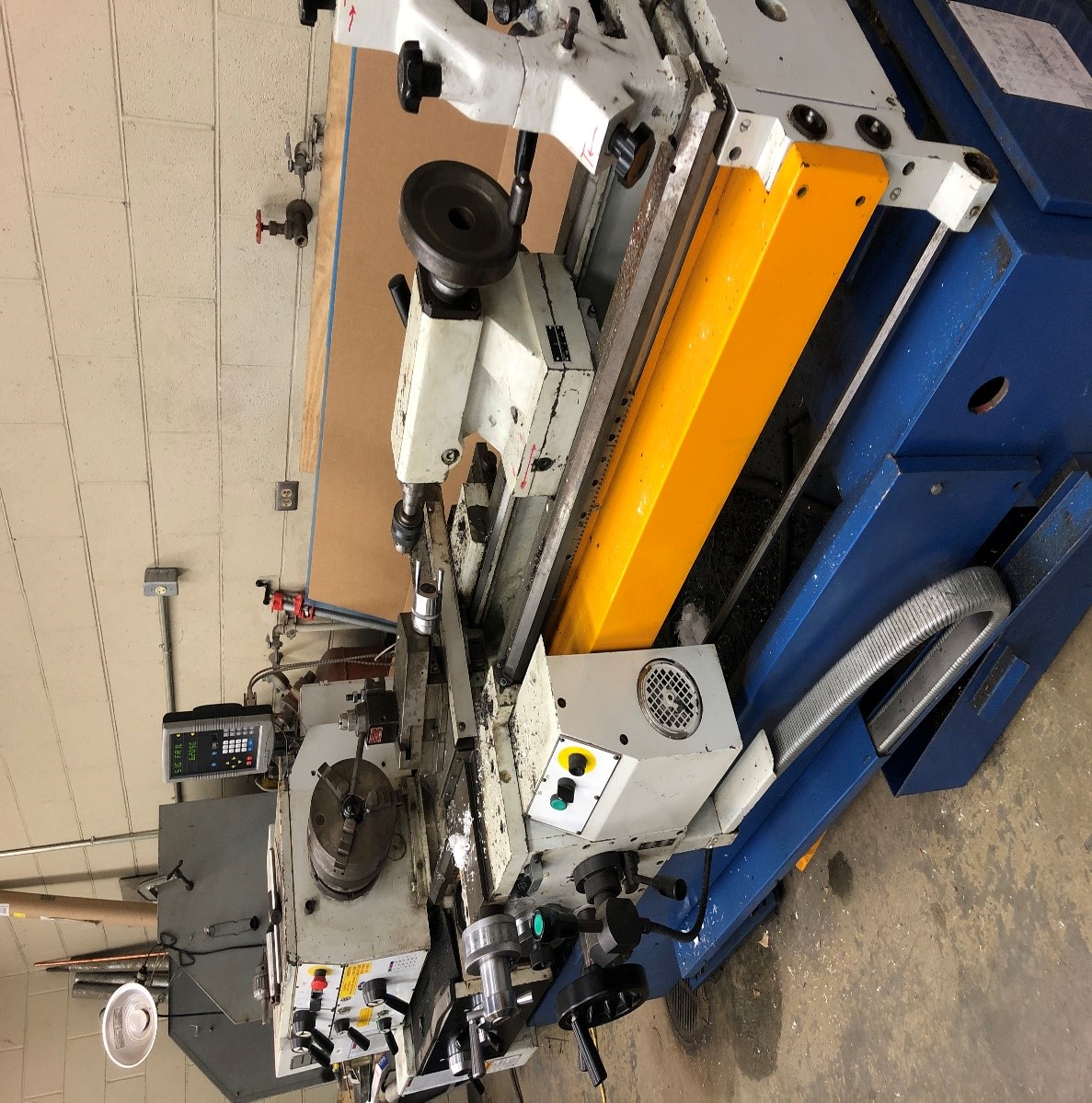
The Texas A&M University-Kingsville provides resources and services to faculty, staff, students, and guests. The university has high-speed data communications, with wireless access available over the campus. All classrooms within the college have teaching stations with computer-based instructional technology including LED projectors. Two of the classrooms have back-projection screens with full multimedia and TTVN (the wide-area data and interactive communications network that serves the campuses and agencies of the Texas A&M System) capability, allowing students to virtually attend classes from remote campuses. Many classrooms serve double-duty as computer labs, allowing students access to a full range of engineering computational and graphics tools. These services are supported through the iTech department dedicated to providing services necessary to acquire, install, maintain, develop and operate the Computing, Telecommunication and Distance Learning systems of Texas A&M University-Kingsville (TAMUK) with microcomputer services, network services, telecom, administrative support, help desk, and distance learning & instructional technology support.
The Mechanical and Industrial Engineering Department at the Texas A&M University-Kingsville (MEIE TAMUK) has excellent analysis and simulation capabilities through a variety of well-proven software packages. Matlab, Visual Basic, C++, and Fortran are used by all faculty. AutoCAD is used for 2D drawing and SolidWorks is for designing 3D dimensional objects, and for basic stress, fluid, and thermal analysis. For manufacturing processes (CNC), Sprutcam, and MasterCAM for SolidWorks are available. The simulation packages ANSYS Workbench and AutoDesk Nastran In-CAD are available for nonlinear static, dynamic, and thermal finite element analyses. For computational fluid dynamics, SolidWorks Flow is used for quick and fast predictions of fluid behaviors, and ANSYS FLUENT is used for higher precision results. The EES (Engineering Equation Solver) package is used for thermodynamics, fluid mechanics, and heat transfer to obtain thermal and fluid properties by handling sets of equations and variables at the same time.
TAMUK, along with the College of Engineering has moved away from standalone PCs to a Virtual Desktop Interface (VDI). A Thin Client is used to access images specific to each department. VDI Server consists of Dell PowerEdge servers. The server systems are attached to a Cisco SSD Flash Drive Storage Array.
Summary of Computer Labs within the College of Engineering.
Building and Room Number |
Number of Student Computer Stations |
Building and Room Number |
Number of Student Computer Stations |
McNeil 308 |
20 |
Sam Fore Hall 111 |
24 |
McNeil 310 |
33 |
Sam Fore Hall 112 |
36 |
ENGC 103 |
14 |
Rhode Hall 244 |
24 |
ENGC 104 |
25 |
Kleberg AG 141 |
28 |
ENGC 106 |
25 |
Eckhart Hall 153 |
24 |
ENGC 218 |
23 |
Eckhart Hall 253 |
24 |
ENGC 240 |
20 |
Manning Hall 212 |
15 |
ENGC 275 |
60 |
SPEC Room 121 |
8 |
Gross Hall 108 |
36 |
MSUB Hallway |
5 |
Gross Hall 109 |
36 |
Jernigan Library |
81 |
|
|
Business Administration 107 |
42 |
ENGC: Engineering Complex
Listing of Software Accessible in Engineering Classrooms/Labs.
Location |
Software |
All classroom and computer lab PC’s |
MATLAB 2020 |
AutoCAD 2020 |
|
Solidworks 2020 |
|
Ansys 2020 |
|
Microsoft Visual Studio Express 2020 |
|
Microsoft Office 2016 |
|
Materials Science Lab |
ExceLINX |
Online - used with MEEN3344 Materials Science course |
WileyPlus online software |
Manufacturing Processes Lab |
Flash-Cut CNC |
Composites Lab |
FibergrafiX Plus |
Controls Lab |
Quanser DAQ Software |
Design and Simulation Lab |
Alpha, beta, gamma radionuclide source set |
The instructional laboratories are taught by lab managers and/or teaching assistants who are trained on the equipment and safety procedures that are used in the classroom. In general, the lab managers train the laboratory teaching assistants on the use of the instructional equipment, and the lab managers and teaching assistants instruct the students.
During the training sessions, safety topics are addressed. The safety topics include eye protection, appropriate attire, burn potentials, locations and how to use eye washing stations, Material Safety Data Sheet (MSDS) information location, and emergency preparedness. The students are guided on safety through demonstration by the lab managers and teaching assistants during the lab class period.
The following are the Standard Administrative Procedures set by the Office of Responsibility of the Texas A&M University-Kingsville.
- Each department that has students enrolled in classes outside of the lecture setting such as teaching laboratories, clinics, etc. where there are potential hazards requiring students to be trained in the safe use of the equipment and/or safe working practices, shall ensure, in conjunction with EHS, students complete the online lab safety training course, delivered through the Blackboard Learning Management System (LMS) no later than the 12th class day of each long semester and no later than the first calendar week of Summer terms and inter-sessions. Failure to complete this training will result in the student being dropped from all courses associated with a laboratory function. This training is valid for one calendar year and is tracked through the Blackboard LMS.
- Each department that employs students to conduct work that would normally require employee safety training such as that offered through the Texas A&M University System’s TrainTraq program shall develop and or assign, in conjunction with Human Resources student-worker safety training specific to the hazard and the environment.
- The Department identifies teaching and/or working environments and duties that require specific safety instruction and documents all student-work safety training within TrainTraq.
- Environmental Health & Safety Department assists with identifying teaching and/or working environments and duties that require specific safety instruction with the development of safety training and monitoring compliance with this procedure.
The use of the computer and computer programs are described in the labs where they are required. Many of the programs are available to the students because of site licensing arrangements through the university. These come with manuals, electronic help, or the students can download instructions from the web.
There is sufficient funding for the maintenance and operation of the experimental equipment in the teaching laboratories. Also, the electronics that support teaching in each classroom are well supported. Money for the updating and systematic replacement of computers is also available.
Each year Higher Education Fund (HEAF) monies are made available for major equipment purchases and large maintenance and upkeep expenditures. The Chairs in the conference with the Dean decide how the HEAF monies will be expended. The expenditures are based on perceived needs rather than a blanket allocation to each department.
Additionally, the department has a machinist to provide manufacturing as needed in support of laboratory equipment and the department also has graduate student assistants to assist the lab managers with the standard installation, maintenance, and management of the labs and their equipment.
The department has a graduate student work-study webmaster to assist with the development and management of the department’s internet pages.
Each lab manager is responsible for the planning and maintenance of the equipment in their labs. The department has a Laboratory Committee, previously chaired by Mr. Daniel S. Wright (who just retired, and has not yet been replaced), which discusses equipment needs and establishes acquisition priorities based on budgetary constraints and the needs of the department. The committee consists of all the lab managers. Equipment acquired as part of an externally funded project is ordered by the project managers without the need for input from the Laboratory Committee. All purchase requests pass through the department chair.
The Jernigan Library was constructed in 1968 as a two-story building (expanded in 1984 to the current three-story structure). The Jernigan Library has 140,000 square feet and features a Library Information Commons (150 workstation areas, 140 workstations, two KIC scanner/printers, six networked printers including one color printer, library/IT service desk), three group presentation rooms, six group study rooms, two library instruction rooms, one University-wide instruction room, and one “smart” instruction room. The Jernigan Library is an open stack library. For ADA users, the library has three ADA electric-powered tables, two ADA manual tables, eight zoom-text workstations, a laptop with JAWS installed, and a Braille manual for JAWS. The library building has an ADA-compliant restroom and is accessible via ramps.
For off-campus users, the library maintains an integrated proxy/catalog server that provides a web presence for the catalog and access to proprietary databases from off-campus. Nearly every online resource is available from any internet-connected computer anywhere in the world (with proper TAMUK credentials). The library has an active interlibrary loan department and is a member of both TexShare programs dealing with resource sharing (courier service and TexShare card program). Jernigan Library patrons can borrow most resources not available from the Jernigan Library, usually at no cost, and are able to use the TexShare card to borrow directly from sister institutions in Texas.
During long semesters, the library is open 100 hours per week (this has been temporarily reduced to 84 hours due to COVID-19). Besides the help available at the two main service points (Reference & Circulation), the library maintains virtual reference help through phone, email, chat, and text. For more in-depth help, the library has a “Book a Librarian” program that can be reserved from a link on the library’s home page. Librarians regularly present instruction in library use throughout the academic year. During the last year for which there is data (2019-2020), librarians presented 84 instruction sessions to over 1,800 attendees. Instruction is presented by request at remote locations (such as the Citrus Center in Weslaco). The library also teaches a one-credit Information Literacy course, normally two sections each long semester. The table below provides a summary of Jernigan Library collections as reported to IPEDS (Integrated Postsecondary Education Data System) in early 2020, which reflects the end of the fiscal year 2019 data
Summary of Information Resources in TAMUK Jernigan Library
Collection |
No. of Items |
Books (title count) |
430,143 |
E-books |
336,771 |
Databases (subscriptions) |
164 |
Media (microforms, AV) |
357,189 |
Media (digital, streaming, etc.) |
87,356 |
Physical serial subscriptions |
391 |
e-Journals, including publisher packages and aggregators |
42,964 |
Currently, there are 151 subscription entries listed on the library’s Online Resources LibGuide (http://libguides.tamuk.edu/onlineresources1), in addition to other databases/websites of academic interest. Among databases of special interest to engineering faculty and students is Academic Search Complete, ACM (Association for Computing Machinery) Digital Library, Annual Reviews, ASABE (American Society of Agricultural and Biological Engineers) Technical Library, ASME (American Society of Mechanical Engineers) Digital Library, Cambridge Journals Online, Computer Source, CRC Handbook of Chemistry & Physics, Credo Reference, Dissertations & Theses Full-Text (ProQuest), Ebooks on EbscoHost, Engineering Village, IEEE Xplore, IOPscience, JoVE Engineering, JoVE Environmental Science, Kanopy (streaming video), Kirk-Othmer Encyclopedia of Chemical Technology, MathSciNet, OnePetro, Science & Technology Collection, ScienceDirect, SciFinder, SpringerLink, Taylor & Francis Online, and Wiley Online Library.
The library’s Javelina Discovery portal (linked to the library’s home page), offers access to the many prints and online resources subscribed to by the library. Javelina Discovery includes all items (excluding suppressed items) from the online catalog, plus most major online resources (principally journal information but also including over 335,000 e-books). Javelina Discovery allows library resource metadata (and often the full text) to be accessed both on and off-campus in a more integrated way than previously available.
Access to materials not held by Texas A&M University-Kingsville may also be requested through Interlibrary Loan. For most of the last half-century, the library has borrowed more than it has lent, but in recent years this trend has reversed and the library now lends more than it borrows. This is almost certainly because of the enormous amount of high-end academic content now available to Jernigan Library users due to piggy-back deals licensed through Texas A&M University.
Reference services are provided in-person and online, through LibGuides created to address specific needs. Faculty can also make requests for library instruction. Library instruction sessions are tailored to meet the needs of a particular class. For example, freshmen may benefit from a general introduction to where collections are housed and how to use the online catalogs, while more advanced students can attend a session on finding technical journal articles and attributing references.
The library has a library liaison program that allows departmental faculty representatives the opportunity to purchase one-time materials for the library. The distribution of funds is based on a formula that takes into account the number of students and faculty in the various University departments and programs.
Though the library has been open continuously throughout the COVID-19 pandemic, some areas have reduced functionality or are closed due to social distancing requirements.
Instructors and lab managers deliver students hazard-specific safety training as appropriate to address hazards of work practices, materials to be used, within the working or learning environment prior to the student being exposed to the hazards and also manage and maintain laboratory equipment. The lab managers and teaching assistants check instructional laboratory equipment for safety concerns before the students run an experiment or use the machine, including looking for frayed wires and other possible shock hazards, checking and maintaining attachments of moving parts, and any other potential issues that may arise from students using equipment in the labs. The teaching assistants are also made aware that they should report any potentially dangerous procedures to the lab managers. General safety procedures are provided on posters in the labs to increase the students' awareness of safety.
Mohammad Alam and Rose Anna Gomez, Building Emergency Managers (BEM) serve as emergency contacts for all activities in Engineering Complex Building.
List of Equipment
Laboratory |
Equipment |
|
Air Velocity Meter & Calculator |
Pneumatics Systems |
|
Air Compressor |
|
Weight Balance |
|
Saybolt Viscometer |
|
Dead Weight Pressure Calibrator |
|
LVDT Measurement |
|
2 Arduino Boards |
|
Venturimeter |
|
Gravimetric Bench |
|
Gear, Pulley, and Slider Crank Arrangements |
|
5 National Instrument Elvis Stations |
|
5 Computers with NI Elvis and LabView software |
|
Materials Science Lab |
Riehle Impact Test Machine model P1-2 |
MTS Universal Testing Machine C45 |
|
TecQuipment Creep Measurement Apparatus model SM106 |
|
Budd Instruments Division Reverse Bending Fatigue Test Machine, 120 in-lb capacity |
|
Fatigue Dynamics, Inc. Torsional Fatigue Tester model LFE150 |
|
Buehler |
|
Buehler Isomet 2000 Precision Saw |
|
Buehler Surface Grinder |
|
2 Buehler Bakelite Presses |
|
5 Buehler Polishing Stations |
|
Struers RotoPol 25 Auto Polisher |
|
Nikon Epiphot 300 Metallurgical Microscope |
|
6 Computers |
|
Keithley Multimeter/DAS units, model 2700 with Model 7708 40-Ch, Diff Mux Module w/ Automatic CJC |
|
Centurion NDT Eddy Current Instrument model ED-530 |
|
Sony Color Video Printer |
|
Denver Instruments Co. Digital Scale model XD-8K |
|
Thermolyne Furnace model 48000 |
|
Scratch testing machine |
|
Fluids Thermal Lab |
Hampden Engineering Wind Tunnel: model H-6910 |
Hampden Engineering Convection Heat Transfer Demonstrator model H-6882 |
|
Setaram Thermal Property Analyzer for measuring the thermal conductivity of solid materials: C-Therm TCi |
|
Gunt Hydraulic System Demonstrators: model HM150.11. |
|
Gunt Venturi meter Demonstrators: model HM150.13. |
|
Hampden Engineering 6-Pass Heat Exchanger Demonstrator: model H-6878 |
|
Hampden Engineering Wind Tunnel: model H-6910 |
|
Manufacturing Processes Lab |
3-axis Sherline table-top CNC Machine |
Intelitek Super ProLight CNC Machining Center |
|
Sherline Table-Top Lathe |
|
8 Computers |
|
Composites Lab |
A Three-Axis Entec-CMC Filament Winder With Fiber Tensioner |
33 cubic foot, 400°F Grieve Curing Oven |
|
Self-Healing Cutting Table |
|
Air Compressor |
|
Vacuum Pump |
|
Carver heated platen press w/two 12”x12” platens, heated up to 650 Fº, with a 5.5” stroke, 20 tons clamping force. |
|
OROS 4 Channel DAS, Instrumented Hammer, Several Accelerometers, and “Visual Modal” Software Installed on Laptop |
|
4 Computers |
|
Robotics Lab |
iRobot Programmable Robot |
Pioneer P3-DX Mobile Robot |
|
|
|
Robotic Arm Manipulator |
|
Humanoid Arm |
|
Hexapod Robot Kit |
|
2 Bioloid Robots |
|
Kondo KHR-2HV Humanoid Robot Kit |
|
Hand Dynamometer |
|
Servo Motors |
|
Sensors |
|
5 Computer Workstations |
|
Controls Lab |
Quanser Heat Flow Experiment |
Water Level Control Experiment |
|
DC Motor Speed Control Experiment |
|
Rotary Servo Base Unit |
|
Rotary Torsion Setup |
|
5 Quanser Data Acquisition Boards |
|
PLC Trainer System |
|
Electro-Dynamic Shaker |
|
Keysight Waveform Generator |
|
Keysight Mixed-Signal Oscilloscope |
|
Keysight MXA Signal Analyzer |
|
8 Power Supply Instruments |
|
National Instruments Elvis Station |
|
Light Source Following Antenna System |
|
MakerBot Replicator 2X 3D Printer |
|
Unmanned Air Vehicles (2 Helicopters, 4 Quadcopters, and 1 Hexacopter) |
|
Eagle Tree OSD Pro Pkg with 100A eLogger/Integrated Connectors and GPS |
|
DragonLink V2 Complete Long Range RC System (Tx&Rx 433MHz) |
|
Twin OBSERVER Helicopter w/ 52cc Twin Engine |
|
7 Computers Workstations |
|
Machine Shop |
2 Milling Machines |
6 Lathe |
|
2 Drill Presses |
|
2 Band Saws |
|
Reciprocating Saw |
|
Surface Grinder |
|
Shaper |
|
Arc Welder |
|
Cutting Torch |
|
Belt Sander |
|
Hydraulic Press |